Home Grown: We Test a Watch for Locavore CollectorsBy Mike Disher,
[Article Appearing in the December 2014 WatchTime Magazine]
What do you get when you cross a historical, American-made pocketwatch with a clock made for military aircraft? You’re reading about it right now. The 801 Aircraft, from RGM, the Lancaster County-based watch company owned by watchmaker Roland Murphy, is a past-meets-present creation that completes a unique clock-pocketwatch-wristwatch timekeeping trifecta. The dial and hands were inspired by a clock developed jointly by Elgin and Hamilton during the 1940s for use in military aircraft. Today, the clock is known by the unromantic alphanumeric designation AN 5741-1. The 801 Aircraft’s movement is styled after the one used in an E. Howard pocketwatch produced in 1915. Today, both clock and pocketwatch are collectors’ items. Will the lovechild delivered by Mr. Murphy have the same staying power? Let’s find out.
The dial incorporates many small details. It’s divided into five distinct sectors. The outer edge is slightly raised. Taking one step toward the center, the scale for the minutes and seconds is slightly sunken. The outer hour chapter, displaying the oversize numerals 13 through 24, rests on a broad, smooth band. The center portion of the dial, about the size of a dime, is sunken, and it hosts the a.m. hours and a small “RGM Professional” logo. The twin hour scales take a few minutes to get accustomed to, unless you’re the type who only looks at the hands. At the bottom of the dial, the oversize subsidiary seconds chapter is sunken and snailed. It features a tri-color display, along with RGM’s trademark Pennsylvania keystone logo and “Lancaster, Penna. USA” inscription.
The modified diamond pointer hands are custom-made to follow the design of the AN 5741-1 clock. Though we like the shape and appreciate the historical fidelity, the hands strike us as slightly petite compared with the bold dial elements. We would have kept the diamond shape, but made the hands just a tiny bit beefier.
Despite the busy dial, the white hands provide good legibility. When the sun goes down, the time can be read for 10 hours with eyes well-adjusted to the dark, so the display will get you through the night.

The case measures 42mm in diameter and 12mm thick, including the domed crystal. The complete package weighs in at 86 grams. The bezel is tall but quite thin, showing off the dial to great effect and making the watch appear larger than it actually is. A fine satin finish covers the case, including the space between the lugs. The finish is very well done and catches the light nicely. It also makes the metal appear slightly darker and richer than would a polished finish.
The lugs are long and curved, ending below the caseback, improving the fit against the wrist. The crystals have non-reflective coating on the inside only. RGM does this because, according to Murphy, an AR coating on the outside of the crystal always ends up showing marks.
The oversize crown is simple in design and has no logo or other markings. It’s easy to grasp, but on our test watch, the setting mechanism felt slightly stiff, and we noticed a small amount of backlash, or play. Our test watch was not equipped with stop seconds, but that feature is available on this watch.
Our 801 Aircraft came equipped with a medium brown leather strap with a pleasing mock patina. The strap has seven closely spaced holes, helping to ensure a comfortable fit. The lugs are 22mm apart, and after trying on several pairs of shoes, we can say that this watch looks great on a range of strap types and colors. Black crocodile dresses it up, dark gray leather is casually elegant, NATOs dress it down, and khaki looks great for summer. The RGM buckle is simple and sturdy enough with a satin finish that matches the case, and the engraved RGM logo works well.
On the watch’s flip side, a thin, screw-in bezel surrounds a broad sapphire crystal that provides and expansive view of the movement.
We picked up our test watch at RGM headquarters in Mount Joy, Pa., in Pennsylvania Dutch country, and we had a chance to tour the facility with Murphy to gain some insight into how the watch is made. During our visit, three things stood out: the fact that RGM makes more than 90 percent of the parts in this watch, that a great deal of handcraft goes into each watch, and that RGM is very committed to the “American-made” ethos.
The movement powering the watch, Caliber 801, begins life as letter-size sheets of nickel silver, also called German silver. The sheets are different thicknesses, because the mainplate is thicker than the bridges. RGM sends the sheets to a nearby company that uses water jets to cut the sheets into playing-card-size pieces. These become the work-pieces from which the mainplate and bridges will be cut. RGM drills precise holes in the work-pieces to locate them on jigs that RGM also makes itself. These holes often have to be hand-broached to ensure a perfect fit. Murphy pointed out that when people think of movement manufacturing, they often overlook the amount of time spent making jigs and tools, getting work-pieces ready to be cut, and otherwise preparing for the machining and finishing that people typically associate with movement making.

The machines that turn the small metal work-pieces into mainplates and bridges were made in the U.S. Most are produced by Louis Levin & Son in California. Another family-owned company in Florida creates custom machines, and RGM itself customizes machines to meet special needs. RGM also makes the tools these machines use. Most of RGM’s machines are the bench-mounted variety, not the larger free-standing machines seen in Swiss or German factories. RGM’s small-scale operation has a more personal feel than those factories do.
One of the RGM-modified machines cuts teeth in the wheel blanks RGM produces. A technician loads five or six wheel blanks at a time, and each tooth is cut individually using an index system to guide the process, assuring that each tooth is identical.
RGM also does its own traditional heat treating and bluing. This in-house process is primarily for small batches of parts, such as those needed for prototyping or repairs. Larger batches, such as the screws for the 801 movement, are sent to a company just down the road that uses a vacuum chamber to produce extremely clean heat-blued parts.
RGM’s commitment to handcraft and bench work is partly a byproduct of the building the company calls home. That building, a former bank headquarters, is historic and quite elegant, but also a bit cramped inside. Narrow doors and stairways keep large machines out, and large machines tend to be the most highly automated. The only sign of automation we say during our visit was a pair of breadbox-size CNC machines that pick up their own tools. Otherwise, hands-on human involvement is the order of the day.
Once the mainplate and bridges are cut, the real handwork begins. On the main floor, we watched a technician tapping screw holes in the 801 mainplate. He did this one hole at a time, with a small, hand-operated tap. Later, the screw holes in the bridges will be countersunk and polished. Blue enamel paint is hand applied to the engraved lettering on the plate and bridges. We were surprised to learn that this step is completed before surface decoration, such as Geneva stripes, is applied.
Caliber 801 has very nicely polished anglage. RGM makes its own tools to hold each bridge as this work is done. The tools reminded us of X-Acto knife handles. Each bridge has its own tool.
Applying the surface decoration is the final step in the finishing process. Each bridge is finished individually, by hand, because tiny variations in thickness can affect the process. Murphy said, “People think we finish all the bridges together – that it’s just zip, zip, zip, and they’re don. That’s not how we do it. It’s one bridge at a time, and it’s a pretty long process.” An indexing system on the finishing machine assures that the Geneva stripes line up when the movement is assembled.
Caliber 801’s bridges were inspired by those of the pocketwatch made in 1915 by E. Howard Co., also called Keystone Howard (the Keystone Watch Case Co. had bought the rights to the E. Howard name some 12 years earlier). When the watch was new, it was priced at $350 – an expensive watch for the day. Murphy spent years tracking down a pristine example, and today it resides in the room-size safe on the building’s main floor.
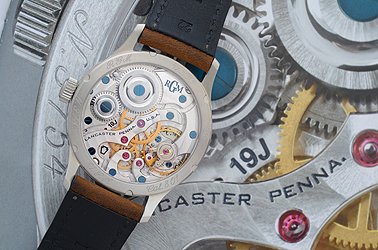
The high level of handwork and the lack of automation allow RGM to offer a wide range of customization options – far more than most manufacturers provide. Murphy told us he does not keep an inventory of assembled 801 Aircrafts on hand for people to walk in and purchase, because there is no “stock” model. If you put down a deposit on an 801 Aircraft today, it will be delivered in two to four months, built just as you like. RGM’s staff of five watchmakers and two technicians currently produces 60 to 70 Caliber 801 movements per year. This is a significant percentage of RGM’s total annual production, which Murphy told us runs 200 to 250 pieces per year.
Our test watch features bridges decorated with côtes de Genève circuilaire and rhodium plating. As noted, the bridges have well-executed anglage, which is not mean feat given the variety of shapes they present. The large screwed balance keeps time at 18,000 vph. The mainplate is decorated with perlage, and peering through the wheels and bridges, we can see an engraved and painted keystone logo, the movement number, and the “19 jewels” notation.
Our test watch kept good time on the wrist, gaining 4 seconds over 24 hours. On the Witschi machine, the results were consistently in positive territory. The greatest deviation was 5.2 seconds (+7.1 dial up, +1.9 seconds dial down). The average deviation was +4.9 seconds – almost exactly what we saw on the wrist. The complete timing results appear in the Specs box.
If you want something unique, RGM’s 801 Aircraft is hard to top, especially given the customization options. The distinctive look, the home-brew movement, the range of options, and the American origin are all unusual. In our view, these factors make it a very appealing package.
SPECS
RGM 801 AIRCRAFT
Manufacturer: RGM Watch Co. 801 W. Main St., Mt. Joy, PA 17552
Reference number: 801A
Functions: Hours, minutes, subsidiary seconds
Movement: RGM Caliber 801, 121 components, manual winding, 18,000 vph, 19 jewels, flat Nivarox 1 balance spring, Incablock shock protection, power reserve = 42 hours, diameter = 36.6 mm, thickness = 4.4mm
Case: Three pieces, stainless steel, screw-in caseback, sapphire crystals with nonreflective coating on the inner surfaces, water resistant to 50m
Strap and clasp: Leather strap with stainless-steel pin buckle
Rate results:
Deviations in seconds per 24 hours
Dial up + 7.1
Dial down + 1.9
Crown up + 6.5
Crown down + 3.5
Crown left + 5.2
Crown right + 5.0
Greatest deviation of rate 5.2
Average deviation + 4.9
Average amplitude
Flat positions 316°
Hanging positions 304°
Dimensions: Diameter = 42 mm, height = 12 mm including crystal, weight = 86 g
Variations: With red dial accents; on bracelet ($7,950); with red dial accents on bracelet ($7,950)
Price: $7,400
Timing tests performed by Wempe Jewelers, New York City